July 2008 Edition
hot markets review: robotics
Robot team shares load ...
... and brings 21st century savings to 100-year-old auto partsmaker
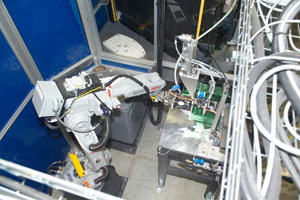
In
Cell 1, an operator loads a part onto an indexing turntable, the turntable
rotates the part into the robot, which moves the part to the terminal
insertion station, and then places it back onto the turntable.
Ask a metal industry robot how it likes working alongside a human
and it won’t answer. The human, however, might have a comment, but
when the robot is saving material and labor, improving quality, and
running faster cycles, it’s hard to have anything negative to say.
That’s the situation Motoman Inc. brought to Grote Industries.
Grote, of Madison, IN, installed two modular, highly flexible robot
work cells that feature robot teams working in close proximity with
human operators.
"Material savings alone easily paid for the robot cells," says
Tom Blades, plant manager. "We also had direct labor savings,
quality improvements, and improved aesthetics," he adds.
A privately owned 100-year-old company with a history of
innovation, Grote was experiencing high demand for components from
automotive,
OEMs and aftermarket suppliers. Grote manufactures head and tail
lamps, dome lights, emergency lighting, flashers, and LED marker
lamps.
The die was cast for Grote to implement robotic assembly to
improve productivity.
"Five or six operators per shift were needed to run these parts
on a manual line and, depending on the product being run, cycle time
was 19-24 seconds per part," Blades says. "With the robot cells, we
only need two operators per shift, and cycle time is 12-15 seconds a
part, so we can run parts nearly twice as fast."
Among the several points that sold Grote on Motoman was its small
footprint.
"This plug-and-play arrangement for the welders saves on floor
space and auxiliary support equipment," Blades says.
Automating the process also has provided quality
improvements, ranging from the cosmetic look to the traceability
with laser-etched identifiers.
Automating the process also has provided quality improvements,
ranging from the cosmetic look to the traceability with laser-etched
identifiers.
"The cosmetic look of the parts is much better now that they’re
being built by robots," says Ed Sitarski, product development
engineer. "We also have improved traceability. Parts are
laser-etched with identifiers indicating the date, time and shift
they were built," he adds.
"Each robot cell can run 10 different parts, and we have 10
product types, each with two color variances (red and amber),"
Sitarski says. "We have three different types of packaging — bags,
totes and boxes. So we have about 60 part numbers that we can change
over to, as needed."
Changeover requires less than five minutes.
The automated system includes multiple processes: inserting
terminals into housings, soldering printed circuit boards (PCBs) to
terminals, dispensing encapsulant material, curing the encapsulant,
welding the plastic lens to the housing, etching, greasing,
labeling, and final testing. Multiple automated inspections are
performed, including vision system checks.
Cell 1 includes three Motoman six-axis HP6 robots equipped with
custom grippers. Quick-change fingers enable the grippers to handle
various part types.
Using a Motoman MSR-500 three-position rotary turntable and part
fixtures at each station minimizes floor space requirements and
simplifies the process. The table is separated into three stations:
operator, soldering/potting, and terminal insertion.
The
Motoman HP6 robot in Cell 2 removes the part from the plug-and-play
ultrasonic welder and transfers it through a series of grease, laser
etching, final test, and labeling operations
Following production of the Cell 1 subassembly, parts are indexed
back to the operator, who then picks up an individual cured lamp
base, adds a lens, and places the part into the Cell 2 fixture. One
operator tends both load stations at Cell 1 and Cell 2.
Curing time is much shorter with the new, less-expensive
encapsulant, which has significantly improved physical properties
and also creates less fumes, making it safer.
Cell 2 uses one Motoman HP6 robot to perform the welding, grease,
laser etch, final test, and labeling processes.
Vibration, ultrasonic and spin welders are mounted on a welder
anchor rail for interchangeability. The different welders are
changed out, as required, depending on the type of part being run.
The graphical user interface screens on the Human Machine
Interface (HMI) actually use visual overlays of the cell with touch
screens that allow users to navigate easily through different
layers, from an overview of all cells to individual cells, to
individual components.
"We can use the HMI to control all part changeovers, diagnose
faults, adjust shift information, track production, track rejects,
enter packaging requirements, and access manuals, drawings, et
cetera," Sitarski says.
"The operators are delighted with the control screens and how
easy the system is to run, as well as the ergonomics," he adds.
Motoman Inc.
What do you think?
Will the information in this article increase efficiency or
save time, money, or effort? Let us know by e-mail from our
website at
www.ToolingandProduction.com or e-mail the editor at
dseeds@nelsonpub.com.